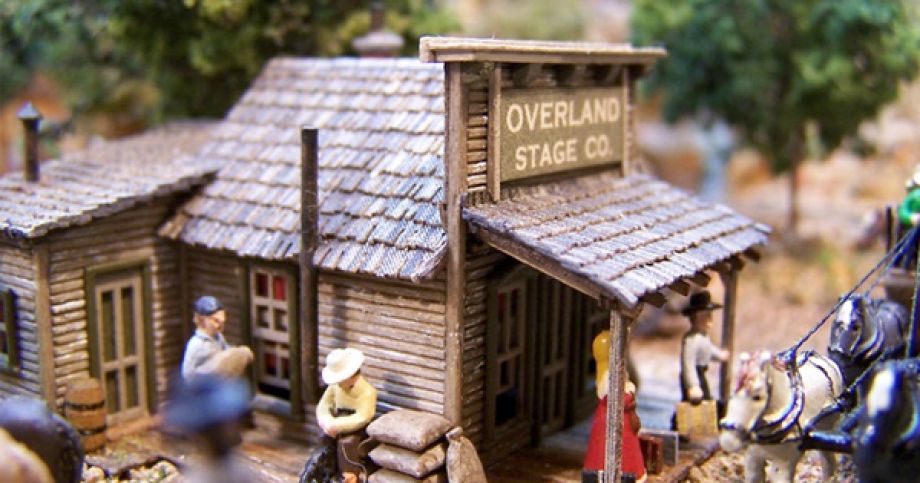
Wild West Scale Model Builders
Architectural model maker utilizes laser for precision and repeatablity in laser cutting
Small business owners are always looking for the next tool or product that will allow them to produce and offer more value to their client base. That’s exactly what Mike Pyne was looking for when he created Wild West Scale Model Builders – a family-owned and operated craftsman kit design/manufacturing company.
After Mike graduated with a master’s degree in architecture, he decided to test his design and modeling skills and go into business for himself. He started Cutting Edge Designs upon graduating and, a year later, Wild West Scale Model Builders. The parent company, Cutting Edge Designs, specializes in museum-quality architectural models as well as graphic design. Wild West Models supplies premium, laser-cut wood craftsman structure kits to model railroaders. The common bond between Mike’s two companies: Epilog Laser.
“When I started producing models for the architectural community and for model railroading, I knew a laser was the key to produce models with unequaled precision and repeatability,” Mike tells us.
“I had some hands-on experience with other laser systems so I knew what they were capable of. I also knew that, just like not all models are designed and manufactured equally, not all lasers are either.
When it comes to service, we know first-hand, that Epilog listens to customer feedback, applies that feedback with new state-of-the-art features and enhancements that keep us wanting every new model because they just keep getting better!
Mike Pyne
“We needed a system to match our precision engineering and design standards. I wanted precise control over the quality of my designs. When it was time to get serious and purchase a laser, I did a lot of research and Epilog came out on top,” Mike said.
“I met Epilog sales representative Ken Crowe at a local tradeshow and after talking with him all afternoon I was invited to Epilog’s manufacturing facility to test files I had created on materials I work with most,” Mike tells us. “It is the absolute best way, and in my opinion the only way, to test a laser system and learn the machine’s capabilities. After spending all day engraving and cutting on every material I brought and just about every other material in Epilog’s sample area, I knew their systems had the best engraving, vector cutting, and speed of any models I had worked with or tested. But as with all things I purchase, I like to know who is going to be there if problems arise, or if I had any questions. This is where Epilog scored second to none.
“When it comes to service, we know first-hand, that Epilog listens to customer feedback, applies that feedback with new state-of-the-art features and enhancements that keep us wanting every new model because they just keep getting better! The service, attention, and education I received were second to none. I learned what types of parts were used in the lasers, toured how they were tested, manufactured, and shipped. It was a company like-minded to my own, so was very relatable.
“Epilog has allowed me to elevate my business and provide a superior-quality product,” Mike said. “Whenever anyone asks me why I selected their product, I tell them precision, speed, design, components, expandability, reliability, innovation, and most importantly, all of the people who stand behind an Epilog Laser system.”