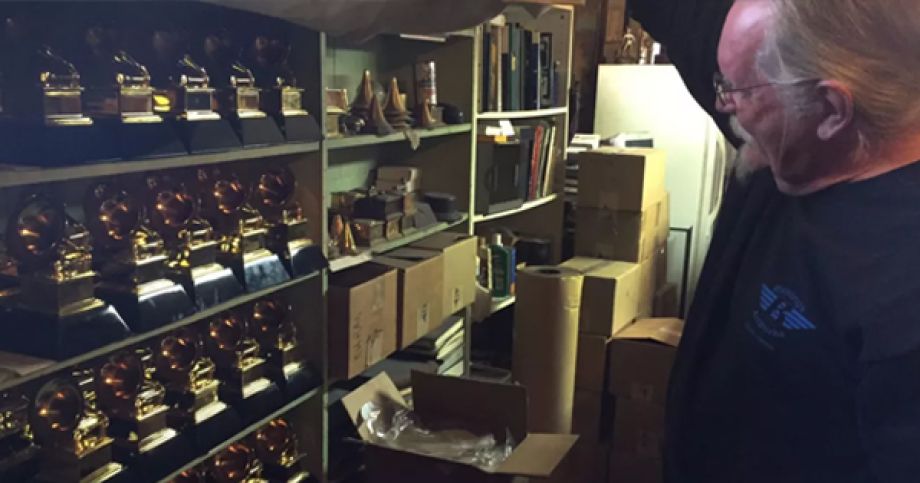
Billings Artwork
Tradition meets technology as Epilog Laser systems help Billings Artworks create Grammy Awards
Established in 1958, the Grammys are one of the most highly-sought after honors in the music business. John Billings, owner of Billings Artworks, has a deep connection to the award as he’s been making them for over 30 years.
“I began working on the Grammys in 1976 in California as an apprentice to Bob Graves, who was a master mold maker,” John tells us. “Bob made molds for metal trophy figures for many of the trophy companies at the time, and he also made the molds for the first Grammy in 1958. After a seven-year apprenticeship, Bob passed away and I bought the business from his widow and moved it into my garage. At that time I was making around 130 Grammys a year and the majority of my work was mold making.”
While the Grammy award itself is created from a mold, the text on the name plaques and serialization tags are engraved. John began engraving the Grammy plates on an antique New Hermes Pantograph. He explains that the machine had a tray of brass letters that the operator would slide into a slot one at a time and then clamp into place. The letters were traced using a stylus with one hand, while the other hand held down a drag-engraving tool that transferred the letters to a brass plate. The process was long and tedious, and John recalls that it was not uncommon to spend as much as three hours engraving just one Grammy.
With my Epilog I have a whole new set of tools and with my creativity and abilities it will take me light-years ahead of my humble beginnings.
John Billings
Realizing he needed to retool the way he went about engraving the awards, John attended his first Awards and Recognition Association show in Las Vegas in 1986. There he found the Dahlgren Wizzard, which he purchased on the spot and used for the last 25 years. Though the Dahlgren drastically reduced the engraving time for John, the size of projects he could do was limited by the small table.
“I was looking for an engraver that would allow me to do larger items,” John said. “I had seen lasers in the industry trade magazines for years, but never thought I could justify the expense. So I started doing some research, downloading manuals, reading the comments and reviews in various forums, and time after time Epilog kept coming out ahead.”
John decided Epilog’s Helix model would best meet his engraving needs. He said after his first job he couldn’t wait to try more projects. “Even before Sean, a representative from Innovative Cutting Systems, came out for our onsite training, I had experimented with all kinds of materials lying around the shop and just kept coming up with new ideas and applications.”
Creating each Grammy from scratch is a time consuming process; however, John’s Epilog greatly reduces the engraving time on several of the components. “When Sean arrived he helped create a jig so that we can engrave 40 Grammy plates at a time – I was very impressed. Additionally, each Grammy gets its own serial number – in the past we would drag engrave a small brass plate and stick it on the bottom. With my Epilog, I cut a jig from Plexiglass and now I can just slip the base of the award into the laser to engrave the serial number and our logo and it’s done in 20 seconds.”
John tells us that currently he is making around 700 Grammys a year and each one has over ten hours work in it. While the Grammy’s take up the majority of his time, he occasionally takes on different engraving and mold-making jobs for other organizations.
“Certainly, the Grammys are the bulk of my engraving but I’m always challenged to do something new and different. I had no sooner unpacked my Helix when I got a call from our volunteer fire department and they needed a plaque for a special presentation. I thought ‘Wow, now I can do something really cool instead of the typical text on a brass plate stuck to a wood plaque.’ I went through some catalogs and found a really nice acrylic plaque, scanned a volunteer fire department logo, picked out a nice font, dropped in the text and I was done. I was very proud of the quality and appearance of the finished plaque and was blown away by how easy it was to create. Of course it helped that I’d spent two months reading the manual and watching the tutorials on Epilog’s website,” John said.
“In the past 34 years I have made over 8000 Grammys, and I still get a humbling feeling when engraving some of the biggest names in the industry. One of my most memorable awards was a Lifetime Achievement Award for Bob Dylan, back in 1991. I was at the ceremony when Jack Nicholson presented the award to Dylan, who I have been a fan of since the early sixties. It was one of my proudest moments,” John said.
As a veteran in the trophy and awards industry, John is able to blend traditional award-making techniques with modern technologies that allow him to be as time and cost-effective as possible. “You rarely see metal figures any more, and molds are now being made machines instead of by hand. When I make a mold some of the tools I use are over 100 years old and were handed down from master to apprentice. With my Epilog I have a whole new set of tools and with my creativity and abilities it will take me light-years ahead of my humble beginnings.”